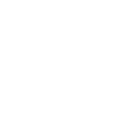
脱泡机新闻
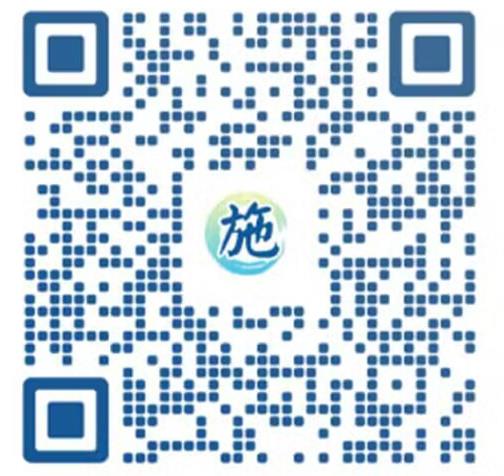
TEL:18925129293
真空搅拌脱泡机在硅碳负极材料中的脱泡应用
日期:2025-04-10作者:小诺在全球加速迈向清洁能源时代的大背景下,硅碳负极材料于锂离子电池领域迅速崛起,已然成为推动行业发展、解锁新能源应用潜能的关键要素。然而,在其制备流程中,气泡问题始终是不容忽视的关键挑战,如同横亘在材料迈向高品质征途上的顽固壁垒。真空搅拌脱泡机作为一项针对性的专业装备,以其精准高效的特性,为攻克这一难题提供了切实可行的解决方案,有力地保障了硅碳负极材料的进阶与发展。
真空搅拌脱泡机工作原理:前沿科技驱动卓越效能
真空搅拌脱泡机作用于硅碳负极材料时,依托一套高度精密且复杂的脱泡体系。其内部结构设计独具匠心,摒弃了传统的桨叶构造模式,转而采用创新性的旋转机制。当硅碳负极浆料,这一由硅源、碳源、粘结剂以及导电剂依据严格比例精准调配而成的功能性复合物,被注入脱泡机腔体的刹那,内置的搅拌系统即刻精准响应。通过巧妙编排的高速公转运动,腔体产生强大的离心力,该离心力仿若一股极具冲击力的高能流体,驱使浆料以极高速度向四周迅猛扩散,致使浆料在腔体壁与内部精密结构件之间发生剧烈的翻滚与碰撞,有效打破了浆料初始的均一性稳态。与此同时,腔体有条不紊地执行精准调控下的自转动作,由此衍生出的剪切力,恰似一组组微观层面的精密刀具,能够精准聚焦于浆料内隐匿的气泡,对那些顽固附着、深藏于材料微观结构内部的气泡实施高效破碎与离散操作,使其彻底丧失聚集稳定性,进而无处遁形。
与之协同运作的真空泵,作为整个脱泡系统的关键辅助单元,如同一位严谨高效的清洁工程师,迅速且持续地抽取腔体内的空气,营造出逼近极限的负压环境。在常压状态下,微小气泡受限于浆料自身的高粘度特性以及表面张力作用,被牢牢禁锢于材料内部,难以实现自主逸出。而一旦处于真空环境之中,外部压力急剧降低,气泡内外即刻形成显著的压差梯度,仿若为气泡注入了强大的外向驱动力,促使其以极高的动能朝着浆料表面快速迁移。最终,这些气泡成功克服表面张力的束缚,顺利排出体系,达成材料深度脱泡净化的目标。公转、自转与真空抽取三者紧密配合、协同联动,共同为硅碳负极材料的品质升级筑牢根基。
助力硅碳负极材料性能实现突破性提升
电化学性能显著优化:气泡在硅碳负极材料微观结构中相当于无序分布的 “阻隔节点”,严重阻碍锂离子在充放电过程中的传输路径,致使电池的充放电效率显著降低,容量发挥亦受到极大限制。经真空搅拌脱泡机精细处理后,材料内部结构得以重塑,呈现出高度紧密且规整有序的状态,为锂离子提供了畅通无阻的迁移通道。在此情形下,电池的首次充放电效率得以大幅跃升,由原本受气泡干扰时的 70% 左右,稳健提升至 85% 乃至更高水平,同时循环寿命亦获得显著延长,为新能源汽车、大规模储能电站等对电池性能要求苛刻的高端应用场景,输送更为强劲、持久且稳定的电能支撑。
材料结构稳定性强化:硅碳负极材料在充放电循环进程中,不可避免地会经历周期性的体积 “膨胀 - 收缩” 变化,倘若材料内部潜藏气泡,这些气泡便如同潜伏的 “结构隐患”,极易在体积变化应力作用下诱发材料开裂、粉化等劣化现象,进而导致电池性能呈现断崖式衰退。而经脱泡处理后的材料,凭借其坚实致密的内部结构,仿若铸就了一副坚韧的 “结构铠甲”,能够从容应对充放电过程中的体积变化挑战,始终确保电极结构的完整性与稳定性,保障电池长期维持高效、稳定的运行状态。
加工工艺适配性进阶:饱含气泡的浆料,因其内部复杂的气液两相结构,呈现出极差的流变特性,仿若一团紊乱无序的 “粘性乱麻”,在涂布工序中根本无法实现均匀、稳定地覆盖集流体,致使所制备电极的厚度均匀性失控,电极性能离散度增大。真空搅拌脱泡机凭借其独特的脱泡与流变性调控功能,仿若一位技艺精湛的工艺大师,巧妙优化浆料的流变行为,使其在涂布环节能够顺滑延展、均匀铺展,确保电极厚度的一致性控制在极小公差范围内,性能表现亦趋于稳定均衡。由此,生产良率得以显著提升,废品率大幅降低,有效削减了因工艺适配性不佳所衍生的成本损耗。
实操流程中的关键节点与精细管控策略
浆料精细预混 “前置基础”:精准称量硅源、碳源、粘结剂等原材料,是开启硅碳负极材料制备流程的首要环节,其称量精度需严格控制在极小的公差范围内,以确保后续产品的一致性与稳定性。将上述原材料置入行星式搅拌器等专业预混设备,以低速、平稳的搅拌模式运行,促使各成分充分、均匀地分散与交融,恰似一场精细编排的分子 “协同舞会”,为后续脱泡工序筑牢坚实的前置基础。若硅源在预混阶段分散不均,极易在局部区域形成高浓度 “团聚体”,这不仅会显著增加后续脱泡工序的操作难度,更会在材料内部埋下影响最终性能表现的 “隐患因子”。
谨慎入料 “关键衔接”:将预混完毕的浆料视作高精密科研样本,以缓慢、平稳且精准的操作手法倒入真空搅拌脱泡机,极力避免因仓促、粗暴的入料方式激起过多新气泡,从而给后续脱泡流程引入额外的复杂性。与此同时,需以严谨的态度全面检查设备密封装置,确保密封性能达到严苛的工艺标准,杜绝任何一丝真空泄漏风险,切实保障脱泡效果不受影响。
参数精准调校 “核心调控”:依据硅碳负极浆料的特性参数,诸如粘度范围、固含量指标以及气泡含量分布等关键信息,在设备控制面板上进行精细、严谨的参数设定。搅拌速度通常需依据浆料粘度动态调整,一般控制在 500 - 3000rpm 区间内精准取值;搅拌时间则应根据气泡含量及浆料特性按需定制,大致处于 0-10 分钟范围内合理选取;真空度亦需维持在 -99.9KPa 的标准工艺区间内稳定运行。特别是针对高粘度浆料这类具有挑战性的 “特殊样本”,需适度延长搅拌与脱泡时间,以确保实现深度脱泡效果。
实时动态监测 “过程护航”:脱泡过程中,透过设备配备的高透明度观察窗,宛如启用一台高精度显微镜,目不转睛地实时观测浆料的动态变化。倘若发现浆料翻腾异常剧烈,仿若陷入 “无序混沌” 状态,或突然出现翻腾停滞、“偃旗息鼓” 迹象,需立即依据专业判断精准调整相关参数,如同经验丰富的船长依据海面实时状况灵活掌舵;同时,需持续关注真空度数值变化以及搅拌电机的运行参数稳定性,确保设备整体运行状态如同定海神针般稳固可靠。
安全出料 “收尾保障”:当达到预定的脱泡时间节点,需耐心等待真空度数值如同精准归位的指针般恢复至常压状态,随后以极度谨慎的操作开启出料口,收集脱泡后的优质浆料。此时,浆料应呈现出细腻、均匀且肉眼难觅气泡踪迹的理想状态,即可满怀信心地将其输送至后续电极成型工序,开启新一轮的高效制备流程。
随着全球清洁能源需求的持续攀升与技术迭代加速,硅碳负极材料产业正搭乘时代发展的高速列车,向着更为广阔的发展空间全速迈进。真空搅拌脱泡机凭借其卓越的脱泡效能与对材料性能的深度赋能,已然成为推动这一产业蓬勃发展、助力行业攀登技术高峰的核心关键装备之一,为新能源领域的可持续发展注入源源不断的动力。